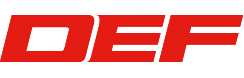
DEF
France
Expert in fire detection / fire safety solutions - Tel (+33) 1 60 13 81 81
En savoir plusAccidental or uncontrolled gas emissions can have serious consequences for the health and safety of people, property and the environment. Gas detectors play an important role in controlling the risks of fire, explosion and the emission of harmful substances.
Gas detection to fight
against an invisible enemy
Gas detection consists of continuously analysing the environment for too high (or too low) a concentration of one or more gases for which they have been programmed.
Releasing too much of these gases can cause fires or explosions. The most common substances in this category are hydrogen (in battery rooms), butane, propane and methane (in rooms with boilers). There are also flammable vapours from solvents and hydrocarbons.
Exposure to these gases can be harmful even at very low concentrations. It can lead to poisoning or even death of those exposed. Examples include ammonia (machine rooms for freezing and fertilizer manufacturing), hydrogen sulfide (refinery, water treatment) and carbon monoxide (underground parking).
Although oxygen is a vital gas, it can be harmful or even fatal to humans in too low a concentration, but also in too high a dose. This is known as anoxia and hyperoxia.
Installation required by insurance companies
The installation of gas detectors is not compulsory. However, it is required by insurance companies in high-risk sectors (see table of applications).
The decision also rests with the head of the establishment, who is responsible for the safety of his or her premises. An accident could cause very serious damage, including loss of life and the destruction of buildings.
ATEX zoning
The ATEX standard governs, at European level, the protection of workers in areas where there is a significant risk of explosion due to the presence of flammable materials. It categorises each zone according to its degree of risk – from 0 (permanent danger) to 2 (rare danger).
Gas detection sensors are installed in areas 1 and 2. They must be ATEX certified.
The level of security integrity
Standards IEC 61 508 and EN 62061 have given rise to SIL (Safety Integrity Level) levels ranging from 1 to 4. These levels are a measure of the performance or reliability of systems with fire safety or gas detection functions.
For gas detection, all sensors must achieve SIL 2 level.
INRS guides
The INRS (Institut national de recherche et de sécurité – National Research and Security Institute) has published guides for estimating the specific gas concentration limits for each product and calibrating sensors accordingly. – For flammable gases, we talk about LELs and UELs (Lower and Upper Explosive Limits of these substances). – For toxic gases, we talk about ELV (Exposure Limit Value over a maximum period of 15 minutes) and AEV (average exposure value over a period of 8 hours).
The oxygen content is expressed as a threshold in %, with 21% being the ideal concentration.
Gas detection is particularly well suited to industrial environments. More broadly, it concerns all sectors of activity where there is a permanent residual presence of gas (pharmaceutical laboratories, food processing plants, water and waste treatment sites, etc.).
Each business sector has its own risks associated with uncontrolled gas emissions.
….
……………
Applications | Flammable gases | Toxic gases | Oxygen |
---|---|---|---|
Heating | X | ||
Local batteries | X | ||
Industrial cooking | X | ||
Laboratory | X | X | X |
Water treatment | X | X | |
Food | X | X | |
Paintings | X | ||
Pharmaceuticals | X | X | X |
Waste treatment | X | X | |
Chemistry and Petrochemistry | X | X | X |
Metallurgy | X | X | |
Energy | X | X | |
Data center | X | ||
Refinery and Gas | X | X | X |
Parking | X | X |
The different types of sensors
The sensors continuously analyse the presence of gas in an area according to a number of criteria: the type of gas to be detected and the level of concentration.
There are different technologies, each associated with the detection of a specific gas. A sensor can be equipped with one or more of these technologies:
.
Calibration bottle
Used during sensor commissioning and maintenance, the calibration bottle is used to calibrate the detectors so that they are perfectly matched to the concentration (% LEL measurement) and gas to be detected.
The power station
Gas detectors are connected to a control unit The latter may be specific to gas detection or the FSS fire safety control unit.
A gas detection centre can manage up to 2,500 detection points depending on the needs of the site to be monitored (1 to 2 points for a small boiler room, around 30 for a pharmaceutical laboratory, up to several hundred for a refinery).
It activates the alarm in the event of abnormal concentrations and enables the safety procedure to be triggered.
Given the many different types of gaseous agents and the specific characteristics of each, the installation of a gas detection system requires a precise methodology that can be summarised in three stages.
Carrying out a risk assessment (gases involved, ATEX zoning, definition of flash point, etc.). Environmental analysis. Definition of the technology and equipment to be used.
Installation of the sensors, taking into account the correct height depending on the type of substance to be analysed (on the floor, at ground level, on the ceiling). Adjustment of the sensors to the recommended levels using the calibration bottle. Commissioning and checking of safety devices (shutdown, gas valve, low-voltage circuit-breaker, audible and visual alarms, alarm forwarding) ….
Each operator is responsible for defining the frequency of maintenance and calibration of the detectors in accordance with the manufacturer’s instructions: every year for flammable gas sensors, at least every six months for toxic gases. Changing the detectors according to the level of gas in the atmosphere can damage the sensors.
DEF can advise you on the best solutions for your situation and guarantee a compliant installation.
As a manufacturer and designer for almost 30 years, our Oggioni plant offers a complete range of solutions. The diversity of our products means we can adapt to all industrial and regulatory issues. The products comply with ATEX requirements and are SIL 2 certified.
With its dual expertise in fire and gas, DEF has been meeting your fire safety and gas needs for over 60 years. Gas detectors can be connected to their own fire and gas detector control units, as well as to FSS fire safety control units.
France
Expert in fire detection / fire safety solutions - Tel (+33) 1 60 13 81 81
En savoir plusItalie, Europe, France
Production sites for gas detection products - Tel (+39) 3 62 62 91 35
En savoir plus To find out more about our expertise in other countries, click here. |